Gasifier slag mainly contains various oxides such as CaO, SiO2, MgO, AL2O3 and Fe2O3. Oxides Compared with various metal oxides in slag, Cr2O3 has the smallest solubility, indicating that Cr2O3 has a certain ability to resist slag erosion. On the other hand, Cr2O3 can react with AL2O3, Fe2O3, and MgO in the slag and transform it into composite spinel. Forming a dense protective layer can effectively prevent further erosion of slag. Therefore, the corrosion resistance can be improved by increasing the proportion of Cr2O3.
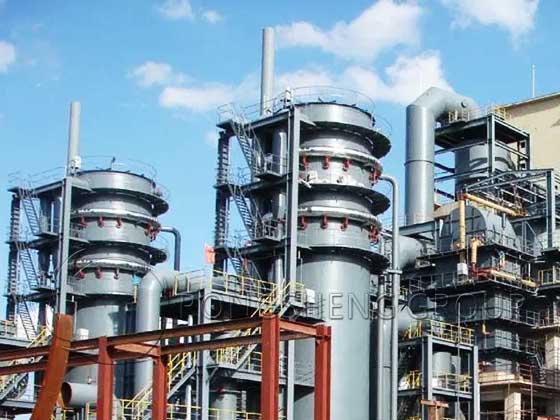
Selection of Refractory Materials for Coal Water Slurry Gasifier
The working conditions of coal water slurry pressurized gasification technology are relatively harsh. First, the combustion chamber temperature in the gasification furnace reaches a maximum temperature of over 1400°C, and the operating pressure reaches a maximum of 8.7MPa. Secondly, the strong reducing atmosphere and high-temperature environment existing in the gasifier will cause erosion to the refractory materials lining the gasifier. Finally, the discharge of liquid molten slagging is accompanied by high-speed erosion of solid, liquid, and gas phases, and there are drastic changes in temperature and pressure during startup and shutdown. Meeting the above working conditions requires high-quality gasifier refractory materials.
The temperature in the gasification furnace is generally higher than the melting point of the slag, so the slag in the furnace exists in liquid form. As the high-speed airflow flows down along the inner wall of the furnace, part of the liquid slag is deposited on the furnace wall, and the other part is discharged from the slag port. Because the liquid slag not only washes away the refractory material of the furnace lining, it also reacts chemically with the furnace lining, thereby eroding the furnace lining. Therefore, furnace lining refractory materials are required to have high erosion resistance and erosion resistance. Due to the high temperature and high-pressure working environment in the furnace, refractory materials are required to have excellent high-temperature creep resistance. High-temperature creep resistance is an important evaluation index of refractory materials. Excellent high-temperature creep resistance can ensure that the refractory materials used in furnace linings will not suffer skin damage during a long period of use.
To sum up, the refractory bricks in the furnace need to meet the following performance requirements. Excellent resistance to slag erosion, high thermal strength, and excellent high-temperature volume stability. Therefore, according to the characteristics of the working conditions in the gasifier, the selection of refractory bricks includes five types of materials: fire-facing bricks, backing bricks, insulation bricks, chrome steel jade castables, and compressible fiber layers.
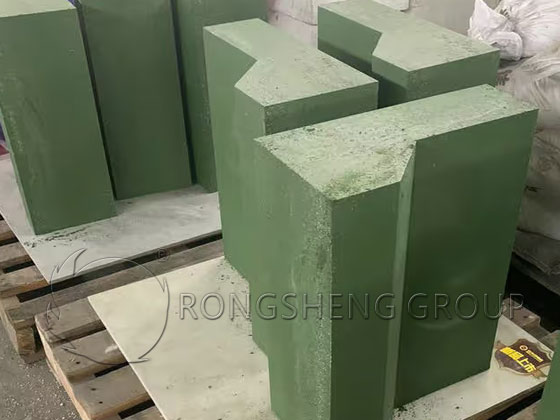
Refractory Layer Erosion Facing Bricks
Due to the large dihedral angle of Cr2O3, there is no wetting effect with coal slag, which can minimize the erosion and penetration of slag. At the same time, because coal slag can directly contact the fire surface, the performance requirements for refractory materials are the most stringent. Therefore, the fire surface bricks of the coal-water slurry gasifier must use high-performance 90 chromium aluminum zirconium bricks, commonly known as high chromium bricks. Preparation process of high chromium bricks. It is mainly made of fused Cr2O3 synthetic material with a purity of not less than 99%, and then adds a certain amount of ultra-fine powder, and goes through processes such as mixing, shaping, and firing in a high-temperature shuttle kiln. The physical and chemical properties of high-chromium bricks are characterized by high volume density, low porosity, high-pressure resistance at normal temperature, and low content of impurities such as iron oxide and silicon oxide. It has the advantages of good thermal stability and high-temperature corrosion resistance.
Permanent Layer Chrome Corundum Brick
Behind the fire-facing brick is the backing brick. Chrome corundum bricks have high strength at room temperature and excellent resistance to corrosive gas erosion. It mainly plays the role of supporting the fire-facing refractory material, and can also resist the erosion of corrosive gases under high-temperature conditions.
Thermal Insulation Bricks
The backing brick is followed by the insulation brick, and alumina hollow ball bricks are generally used as insulation bricks. It has low thermal conductivity and a good thermal insulation effect, which can effectively reduce the heat loss of the gasifier and reduce energy consumption. At the same time, alumina hollow ball bricks have high strength under normal and high-temperature conditions. The material is light has very low impurity content, and has excellent corrosion resistance and thermal stress resistance.
Chrome Corundum Castable
Chrome corundum castable is mainly used for the spherical top and cone bottom parts of gasification furnaces. It has the advantages of good integrity and easy construction. Especially when it comes to the construction of complex structures, using chrome corundum castables is not only convenient and fast, but also saves man-hours. In addition, chromium corundum castables have strong resistance to gas erosion, high volume density, and good air tightness. Therefore, the service life of the gasification furnace can be greatly increased.
Insulation Cotton Layer
Due to its small bulk density and low thermal conductivity, the compressible fiber layer has excellent thermal insulation properties. At the same time, it can effectively reduce the radial expansion of the inner refractory material under high-temperature conditions. On the other hand, compressed fiber layers are very convenient to construct and can save manufacturing costs.
Rongsheng Refractory Materials Manufacturer is a powerful manufacturer of refractory materials production and sales. Our refractory products have been sold to more than 100 countries and regions around the world. There are many application cases for our chrome corundum brick products, and all of them have achieved good use effects. Contact us for a free refractory lining solution and quote.