Lining repair is a common item in heating furnace maintenance work. There are two main methods of repairing linings. One is to use the same refractory castable as the original lining for repair, and the other is to paste a certain thickness of refractory fiber felt. The construction method and quality requirements for repairing the lining with refractory concrete are the same as those for the new furnace lining. In addition, pretreatment of the repair surface needs to be done.
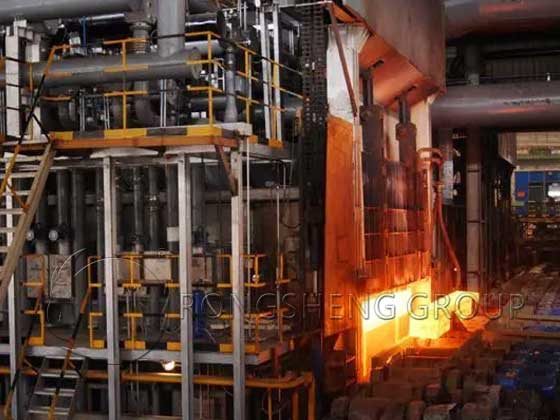
Construction Method of Repairing Lining with Refractory Castable
Commonly used for repairs of lightweight refractory castable linings. Before construction, materials must be prepared, a detailed understanding of the construction site, and construction tools must be cleaned. The specific pre-construction preparations are as follows.
- (1) Before construction, the repair scope should be reasonably determined based on the damage to the lining. Remove the failed furnace lining within the repair range to meet the pretreatment requirements for repair construction.
- (2) Containers and tools used for lining construction should be cleaned. Prevent lime, other cement, clay, and other impurities from mixing into the aggregate.
- (3) Ceramsite should be soaked for at least 12 hours before use, and excess moisture should be eliminated during use.
- (4) The parts of various pipe racks, casings, and other metal components (except insulation nails) buried in the lining should be coated with 0.5~1.0mm thick asphalt.
- (5) The construction site should be maintained between 10 and 25°C, and cooling or warming measures should be taken accordingly in summer or winter. After the curing is completed but not in the oven, the temperature should be kept above 5°C to prevent freezing damage to the lining.
The construction method of repairing the lining with refractory concrete can be carried out in the following three methods depending on the materials used.
1. Smearing method
During construction, the steel wire mesh must be filled with castable. There must be no holes and the concrete must be dense. When applying, spread the concrete and smooth it with a wooden trowel until the surface is rough. To prevent cracks, the castable surface cannot be calendered. This method is suitable for small-area lining repairs.
2. Spray coating method
The semi-dry method should be used for spraying, that is, the refractory material should be properly moistened with water and stirred evenly before adding it to the sprayer. When spraying, the material and water should be sprayed evenly and continuously, and there should be no dry material or flow on the spray surface. The nozzle should continuously move in a spiral manner to distribute coarse and fine particles evenly. Spraying should be carried out in sections and continuously, reaching the thickness at one time to avoid delamination. If the thickness cannot be reached at one time, layered spraying can be used, but the second layer must be sprayed before the initial setting of the previous layer of spray paint. When construction must be interrupted, diagonal stubble should be left at the joints. When construction continues, the joints must be cleaned and moistened with water. During spraying construction, the thickness of the spray coating should be checked at any time. The excessively thick parts should be shaved off, and the surface of the spray coating should not be smoothed. When spraying, a wooden box should be used to leave a test block at the spraying location to check its strength and bulk density. After construction, tap gently with a small hammer to check the density of the sprayed layer. If any holes or interlayers are found, they should be dug and repaired in time. This method is suitable for repairing or constructing new furnace linings in large areas with thick linings (greater than 50mm).
3. Mold pouring
The pouring and loading of the mold into the formwork should be done in layers, and the thickness of each layer should be 150~200mm. In order to prevent the delamination of light aggregate and cement during tamping, which increases the bulk density and affects the thermal conductivity, mechanical tamping should not be used. Manually tamped concrete must be dense and free of honeycombs and voids. When tamping, first tamp around the anchor pin, and then tamp it again with half a hammer, without over-tamping or missing tamping.
Pouring of refractory concrete is best done continuously. When construction must be interrupted, the joints should be “roughed” and covered tightly with plastic film. After 12 hours, pouring can be continued.
When pouring refractory concrete on top of the insulation block, prevent the upper insulation block from absorbing water. The best way is to paint a layer of asphalt on the insulation block, or you can lay a layer of plastic film. If plastic film is spread on a vertical surface, it should be fixed to prevent it from slipping. This method is also suitable for the repair of large-area, large-thickness vertical linings and the lining construction of new furnaces.
Refractory fiber paste repair method
The use of refractory fiber paste to repair the lining is a new method developed in recent years. It has the advantages of simple construction, no need for maintenance, and short oven and maintenance cycles.
When overhauling the lightweight heat-resistant concrete lining of the heating furnace, it was found that the surface of some linings was generally delaminated, powdered and peeled off, that is, the surface layer of the concrete lining lost its strength. The reason for this phenomenon may be the corrosion of the gas medium in the furnace. If you still use raw materials to repair it at this time, you will definitely make the same mistake again. The use of pasted refractory fiber felt is an effective method.
Scrape off the powdery layer on the original lining surface and roughly level it. Large cracks and peeling areas are hand-painted with raw materials, and then a layer of refractory fiber felt is pasted. The thickness of the paste should be determined through calculation, but it should not affect the heating of the furnace tube surface. This composite structure of ceramic fiber felt is vertically attached. The vertical ceramic fiber felt is cut by machine according to the required thickness and tied into bundles.
Before pasting, clean the flattened lining to remove any floating material. When pasting, start from the root of the wall and paste it from bottom to top. Use a paint brush to spread the adhesive on the furnace wall and the ceramic fiber bundle strips respectively, and apply it fully. Then attach the ceramic fiber bundle strips and compact them with your hands. If there is water on the furnace wall or top, the ceramic fibers will not be able to stick to it.
The adhesive should have properties such as high-temperature resistance, strong adhesion, lightweight, and the ability to cure at room temperature. Currently, commonly used adhesive types include:
- (1) Water glass: pulp waste liquid = 1:1 plus 10% clay clinker powder and a small amount of clay powder.
- (2) Aluminum silicate adhesive.
- (3) Methylcellulose.
- (4) Aluminum phosphate adhesive, phosphoric acid: aluminum hydroxide = 8:1.
For example, adding masonry powder to the adhesive to make it into a paste, and adding some MgO can make it stronger at room temperature.
Rongsheng refractory material manufacturers can provide customers with comprehensive refractory material services. Extend the service life of refractory lining materials in high-temperature industrial kilns and reduce the number of furnace shutdowns and repairs. Design and construction of refractory solutions for insulation layers, and turnkey projects of refractory lining materials for high-temperature industrial furnaces. If you are in need of purchasing heating furnace lining refractory materials, refractory brick linings, or unshaped refractory linings, please contact us. Get free quotes and samples.