Jan 24, 2024
Carbon and Graphite Refractory Materials for Metallurgical Industrial Furnaces
Carbon and graphite can constitute refractory materials or serve as important raw materials for refractory materials, mainly based on their following properties.
- (1) Graphite has high heat resistance, and the maximum temperature can reach 3850°C. Graphite has small mass loss in ultra-high temperature arcs.
- (2) Graphite has high chemical stability and is not easy to react with other inorganic materials and molten metals. It is also difficult to be wetted by oxide slag and has strong penetration resistance.
- (3) The thermal conductivity of graphite is large, but it decreases as the temperature increases. Even at extremely high temperatures, it is in an adiabatic state.
- (4) Graphite has an anisotropic structure and a small linear expansion coefficient. Therefore, it has good thermal shock resistance.
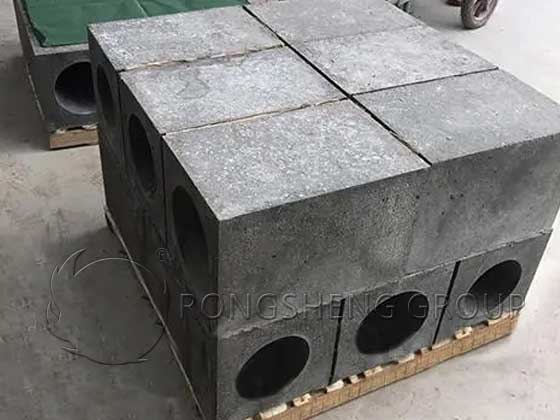
Application Development of Carbon and Graphite Refractory Materials in Blast Furnace Lining
Carbon and graphite refractories have been used in iron-making blast furnaces for a long time and have continued to develop with the development of iron-making blast furnaces. For example, Germany began using carbon bricks in blast furnaces in 1920. Subsequently (in the 1940s and 1950s), various countries competed to use carbon bricks in blast furnaces. Nowadays, large blast furnaces in the world are built with carbon bricks (charcoal blocks) from the furnace bottom, hearth to furnace belly, and other parts. Some blast furnaces are built to the furnace shaft and even the taphole. With the adoption of water-cooled furnace walls, the interior of the blast furnace bell is also built with carbon bricks.
Early carbon bricks mainly used metallurgical coke as the main raw material, asphalt as the binding agent, and were produced by extrusion molding. However, this kind of carbon brick often suffers from local abnormal erosion during use. For this reason, the metallurgical coke was changed to roasted anthracite coke with good resistance to molten iron erosion to improve the performance. However, although roasted anthracite char has the advantage of good resistance to molten iron erosion, it has the disadvantage of poor alkali resistance due to its high ash content. To overcome this shortcoming of roasted anthracite coke, artificial graphite is also used.
In order to reduce the damage of carbon bricks caused by molten iron seeping into the pores, various improvements have been made to carbon bricks.
- (1) To improve the corrosion resistance of molten iron, alumina is added to the ingredients.
- (2) To reduce the pore size, metallic silicon is added to the ingredients. During firing, the reaction generates whiskers, which refine the pores and prevent the intrusion (infiltration) of molten iron.
- (3) To improve the cooling effect, the graphite blending ratio is increased.
- (4) Change the binding agent from asphalt to resin to improve the high-temperature strength.
- (5) By adding SiC, the pores are made fine and the intrusion of molten iron is prevented.
- (6) At the bottom of the furnace, to improve the cooling effect, graphite bricks and C-SiC bricks with high thermal conductivity are used on the outside of the furnace.
The largest user of carbon and graphite refractory materials is the metallurgical industry, which is mainly used for lining refractory materials in blast furnaces (carbon and graphite refractory materials for blast furnaces), ferroalloys, metal refining (including electric furnaces and iron furnaces), etc. Among them, the usage of blast furnaces exceeds 70% (75% in Japan). In steelmaking electric furnaces, the use of artificial graphite bricks in harsh parts can extend the service life. In addition, carbon bricks are used as refractory materials for lining electric furnaces when producing phosphorus and soluble phosphate fertilizers.
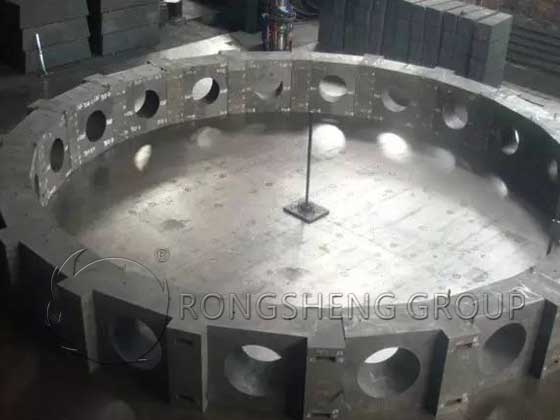
Carbon and Graphite Refractory Materials are Used as Lining Materials for Non-Ferrous Metal Smelting Furnaces
Widely used carbonaceous and graphite refractory materials are amorphous carbon bricks, partially graphite or semi-graphite carbon bricks, and graphite bricks. At the same time, graphite crucibles and carbon amorphous refractory materials are also used in large industries.
In addition, carbonaceous and graphite refractory materials are also used as refractory materials for the lining of non-ferrous metal smelting furnaces. For example, carbon and graphite refractory trees are widely used in aluminum electrolytic cell linings. Typically, aluminum electrolytic cells are rectangular steel shells lined with carbon bricks. There is a carbon anode suspended in the electrolytic cell, and the bottom of the carbon cell is the cathode. Aluminum electrolytic cell cathode materials, need to have good electrical conductivity and be able to resist the erosion of cryolite, NaF, and liquid aluminum at high temperatures (900~1000°C). Therefore, carbonaceous materials are generally used as cathodes in aluminum electrolytic cells.
The damage to the carbonaceous material at the bottom of the aluminum electrolytic cell is mainly due to the infiltration of Na. Followed by the erosion of cryolite (completed through the following reaction):
3NaF·AlF3+Al═3Na+4AlF3
It has now been confirmed that Na penetration decreases with increasing degree of graphitization of the carbon cathode. Therefore, the cathode material of aluminum electrolytic cells is developing from the original amorphous carbon brick to semi-graphitized brick or graphitized carbon brick. At the same time, a layer of coating is applied on the surface of the carbon cathode that has good wettability with liquid aluminum but is infusible or refractory to liquid aluminum and cryolite and has good conductivity. For example, TiB2 or coatings containing TiB2 powder.
Since oxygen is precipitated from the carbon anode, the carbon anode oxidizes quickly and suffers large losses. In order to enable continuous production, it is necessary to continuously add anode paste to the top of the self-baking anode, which is composed of pitch coke or petroleum coke and coal pitch. It is completed by direct current conduction through the anode and heat generated between the electrodes. In addition to self-baked anodes, prebaked anode processes have also been developed.
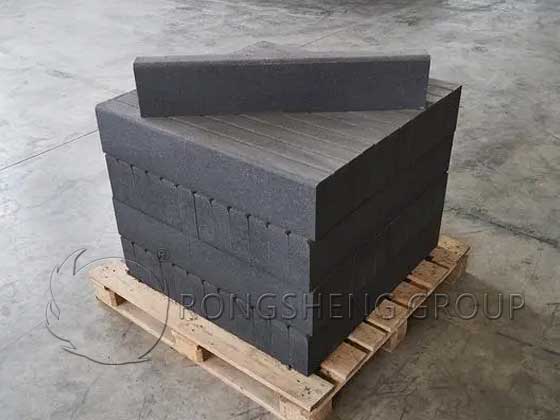
In the past, carbon bricks have been used for the side walls of aluminum electrolytic cells. However, due to damage to the side wall carbon bricks, the service life of the aluminum electrolytic cell was reduced and its normal operation was affected. In order to prevent the side wall carbon bricks from being damaged by oxidation, SiC refractory materials (bricks) were used to build the side walls. These include high aluminum or alumina combined with SiC refractory materials, silicon nitride combined with SiC refractory materials, Si2N2O combined with SiC refractory materials, Sialon combined with SiC refractory materials, and self-bonded SiC refractory materials. SiC does not react with Na3AlF6, AlF3, NaF or CaF2. Among them, silicon nitride combined with SiC refractory materials has high resistance to cryolite erosion, good oxidation resistance, high strength, and high resistance. This can not only extend the life of the electrolytic cell and reduce leakage, but also greatly reduce the thickness of the side wall lining and expand the volume of the electrolytic cell.
RS Refractory Material Manufacturer is a powerful refractory material manufacturer. We are engaged in the production and sales of refractory products. If you need to purchase refractory lining materials or would like to find a suitable refractory lining material solution, please contact us. We have extensive experience in projects where carbon and graphite refractory materials are used in metallurgical industrial furnaces, and carbon and graphite refractory materials are used as lining materials for non-ferrous metal smelting furnaces. Free quote at email inquiry@refractoriesmaterials.com.
More Details