An inorganic thermal insulation board is a new type of refractory thermal insulation material processed by a large-scale automatic continuous production line using pure inorganic materials. The use temperature ranges from 900°C to 1300°C, and it can be used as a backing for various industrial kilns, which is a good solution to the heat insulation problem of the kiln. The bulk density can be processed and produced from 0.35 ~ 0.4 ~ 0.45 ~ 0.5. Under the condition of a working temperature of 350℃, the thermal conductivity can be controlled in the range of 0.11 ~ 0.13, and the strength can be controlled in the range of 1 ~ 2Mpa. It can not only be processed into ordinary shapes but the maximum size can be processed into a size of 1 meter * 2 meters.
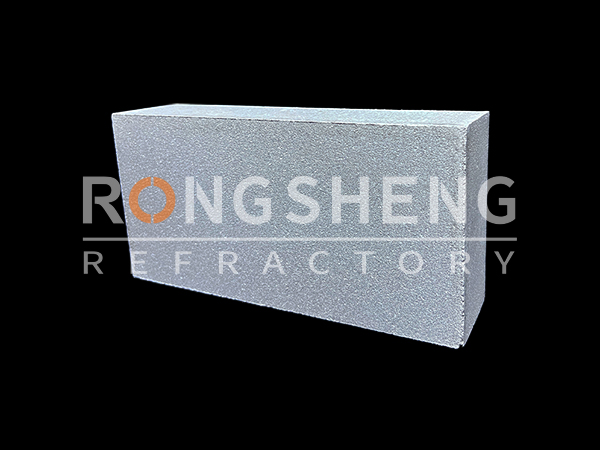
Advantages of Inorganic Insulation Panels
It can be used to replace the following insulation material products, such as a 1260-type aluminum silicate fiber backing board, and 1400 type aluminum silicate fiber insulation board. Advantages of inorganic thermal insulation panels in production and use. In the production of inorganic thermal insulation panels, it is more environmentally friendly and efficient. Its performance is not easy to shrink, not easy to pulverize, small thermal conductivity, no attenuation of heat preservation effect, long life, more energy saving, and higher cost performance.
Main Features of Inorganic Thermal Insulating Boards
Low thermal conductivity, more energy-saving. The composition structure of inorganic heat insulation boards from RS kiln Refractory Factory is composed of nano micropores, so the product has good heat insulation performance.
No shrinkage and small gaps after heating. Within the specified operating temperature, the heating permanent line change rate of the New Inorganic Thermal Insulating Boards is less than 0.5%, and it will not shrink after long-term use. For ordinary thermal insulation boards, the heating permanent line change rate reaches 2%-3% shrinkage. The shrinkage is more than 4 times that of the New Inorganic Thermal Insulating Boards.
Completely free of fiber and organic matter, it can be used for a long time under various working conditions. No chalking, no attenuation.
High strength and wide application range. The New Inorganic Thermal Insulating Boards from the RS kiln Refractory Factory have better compressive strength at room temperature. Compared with ordinary thermal insulation boards, its normal temperature compressive strength can reach more than 3 times, and it also has good strength after burning. Long-term use at high temperatures is more secure and has a wider range of use.
The Inorganic Thermal Insulating Boards have no stimulation to the human body and no pollution to the environment. The construction is convenient, healthy, and environmentally friendly.
RS kiln Refractory Factory Inorganic Thermal Insulating Boards have good quality control and a large production capacity. It is not restricted by environmental protection, and the delivery time is guaranteed.
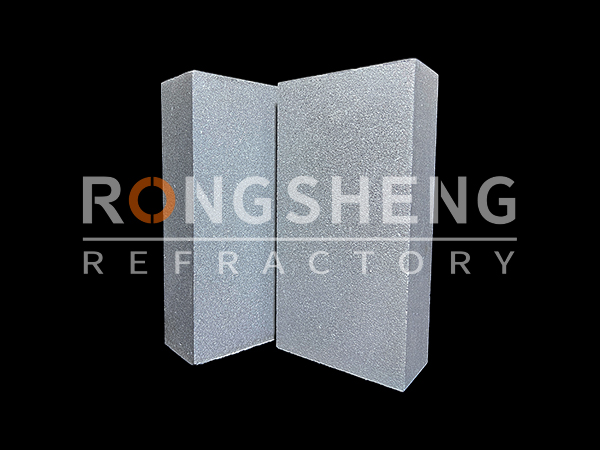
Index Parameters of Inorganic Thermal Insulating Boards
Classification Model | RS-B0.35 | RS-B0.55 | RS-B0.6 |
BD,(g/cm3) | ≤0.35 | ≤0.55 | ≤0.6 |
CCS,(Mpa) | ≥0.8 | ≥2.0 | ≥2.0 |
TC,400℃(W/m·K) | ≤0.105 | ≤0.115 | ≤0.12 |
PLC,% | ±0.5% 950℃×12h |
±0.5% 1050℃×12h |
±0.5% 1250℃×12h |
Dimensional Requirements for Inorganic Thermal Insulation Panels
- Regular size: 400 x 600mm, thickness 30-80mm.
- Special sizes can be customized according to drawings.
Application of Inorganic Thermal Insulating Boards
Inorganic Thermal Insulating Boards products in RS Kiln Refractory Factory can be applied to the following scenarios: backing insulation lining of heat treatment furnaces in the metallurgical industry, steel rolling heating furnaces, and other kilns. The backing insulation lining of kilns such as roller kilns in the ceramic industry; the backing insulation lining of kilns such as calciners in the cement building materials industry. The backing insulation lining of kilns such as electrolytic cells in the electrolytic aluminum industry; the backing insulation lining of kilns such as cracking furnaces in the chemical industry.
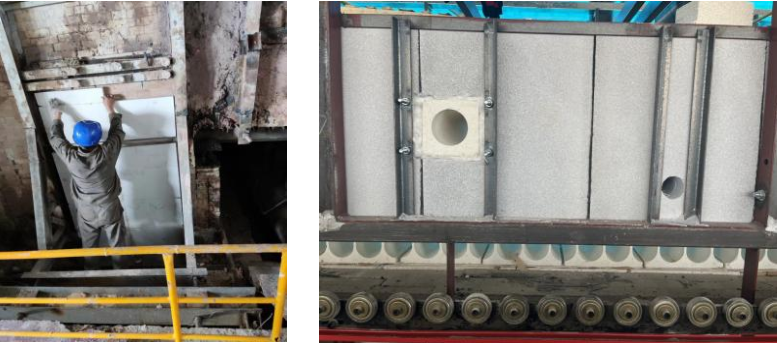
Ceramic industry roller kiln backing plate
- Application location: ceramic roller kiln wall heat insulation backing board, bottom backing heat insulation layer.
- Can be used to replace, 1260 aluminum silicate fiber backing board, and 1400 aluminum silicate fiber insulation board.
- Application advantages: not easy to shrink, not easy to pulverize, not easy to decay in performance, and more cost-effective.
Regenerators for the glass industry
- Application location: wall insulation of glass furnace regenerator.
- Can be used to replace: 1260 aluminum silicate fiberboard, and 1400 zirconium-containing aluminum silicate fiberboard.
- Application advantages: no shrinkage, performance is not easy to decay, all inorganic.
Inorganic Insulation Board for Sale from Refractory Factory
ZZRS Refractory Factory is a team dedicated to refractory lining solutions for high-temperature industrial furnaces. Our customers are located in more than 100 countries and regions all over the world. RS kiln Refractory Factory refractory brick products and insulation products have significantly longer service life than those refractory products that customers have used before. The performance of our refractory products has also been unanimously recognized by customers. Now, our new insulation material products are dedicated to solving the configuration of refractory materials for the insulation layer of the rotary kiln, such as the new Inorganic Thermal Insulating Boards. Reduce the temperature of the outer wall of the industrial furnace, save production energy, and reduce production costs. Contact us to get the price and samples of inorganic thermal insulation panels for free.