Fire Clay Brick Applications
Fireclay bricks are often used in the Metallurgy, building materials, chemical industry, petroleum, machinery manufacturing, silicate, power and other industries.
Shape |
Brick |
Material |
Alumina Cement |
Al2O3 Content (%) |
30% |
Refractoriness(SK) |
32 |
Cold Crushing Strength (MPa) |
25 |
Bulk Density(g/m3) |
2.05 |
Porosity |
2.10-2.15 |
Thermal Expansion At 1000°C (%) |
0.6 |
Size |
Customized |
|
|
Fire Clay Brick Physical & Chemical Indicators
Fire Clay Brick SK-32 |
Item |
Standard |
AI2O3(%) |
30 |
Fe2O3 (%) |
3 |
Refractoriness (SK) |
32 |
Refractoriness under load, 0.2MPa, Ta, ((°C) |
1300 |
Porosity (%) |
22-26 |
Bulk density (g/cm³) |
2.05 |
Cold crushing strength (MPa) |
25 |
Thermal expansion at 1000°C (%) |
0.6 |
Fire Clay Brick SK-34 |
|
Item |
Standard |
AI2O3(%) |
38 |
Fe2O3 (%) |
2.5 |
Refractoriness (SK) |
34 |
Refractoriness under load, 0.2MPa, Ta, ((°C) |
1350 |
Porosity (% |
19-23 |
Bulk density (g/cm³) |
2.10-2.15 |
Cold crushing strength (MPa) |
25 |
Thermal expansion at 1000°C (%) |
0.6 |
Fire Clay Brick SK-36 |
|
Item |
Standard |
AI2O3(%) |
50 |
Fe2O3 (%) |
2 |
Refractoriness (SK) |
36 |
Refractoriness under load, 0.2MPa, Ta, ((°C) |
1450 |
Porosity (% |
20-24 |
Bulk density (g/cm³) |
2.30-2.40 |
Cold crushing strength (MPa) |
45 |
Thermal expansion at 1000°C (%) |
0.3 |
Fire Clay Brick of Furnace Photos for Different Type
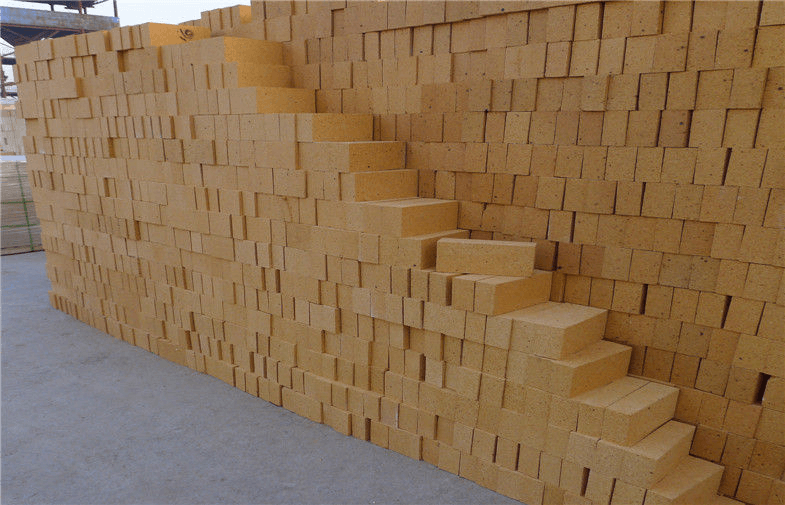
Fire Clay Brick of High Temperature Furnace Packaging & Shipping
Heavy dense fire clay bricks are packed on wooden pallet with papers in each layer and PP film wrapped outside of the whole pallet.
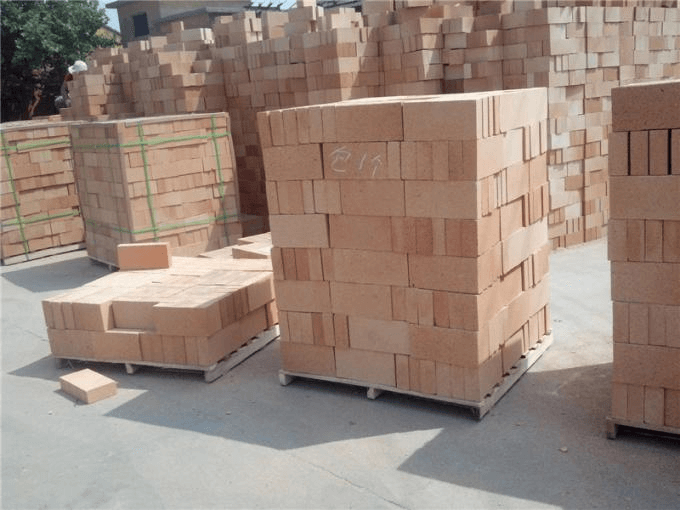
Fire Clay Brick Manufacturer from China Refractory Material Factory – RongSheng
Zhengzhou Rongsheng Refractory Material Co., Ltd. is located in the hinterland of Central Plains, at the foot of Songshan Mountain, and adjacent to Zhengshao Highway, Longhai and Jingguang railways. The convenient transportation, abundant resources and high quality minerals provide favorable conditions for the production of refractory materials.
Established in the early nineties of twenty century, with continuous innovation and development, now it is a comprehensive enterprise in refractory material sindutry, covering metallurgy, building materials, electric power, chemical industry etc.
Our main products: refractory material for industrial furnaces, such as high-alumina brick, refractory fire clay brick, silicon brick, high-strength diatomite brick, light weight insulation brick, low iron mullite brick, etc;anti-stripping alumina brick,alkali proof brick,phosphate brick for cement industry; For the industrial furnace and power boiler, we can provide various series of abrasive bricks,corundum brick, mullite brick, wear resistant castable, corundum castable , high strength low cement castable, impervious material,plastick refractory, etc. Our products are popular in the whole country and have been exported to India, Iran.etc.
RS refractory company adhering to the ” integrity, innovation, hard work” and business philosophy,the ” people-oriented” as the cornerstone of enterprise development, to ” the pursuit of excellence” as the core values of the enterprise, will create ” Rongsheng Brand” as a corporate strategic objectives.and product types rich scientific management processes, improve customer information management system, timely, efficient, to provide satisfactory service to our users.
FAQ
1. Are you a manufacture or trading company ?
Factory+ trade(mainly factories, at the same time, we operates other related products)
2. Can we visit your factory ?
Sure,welcome at any time, seeing is believing.
3. Is your company accept customization ?
We have own factory and excellent technical team, and we accept OEM service
4. What’s the MOQ of trial order ?
No limit, we can offer the best suggestions and solutions according to your condition.
5. Will your company supply samples ?
Yes, we do. The shipping charges should be undertaken by customer.