Oct 12, 2023
Affordable Refractory Plastic Furnace Linings from the Manufacturer
Refractory plastic is a plastic refractory material made by mixing mainly refractory aggregates and powders, adding appropriate binding clay, binders, and admixtures. RS Refractory Materials Manufacturer can provide cost-effective refractory plastic furnace linings. According to the performance requirements of refractory plastic furnace linings, its varieties include clay, high alumina, silicon, magnesia, magnesium chromium, and silicon carbide. The most widely used refractory plastics in soaking furnaces are clay and high alumina.
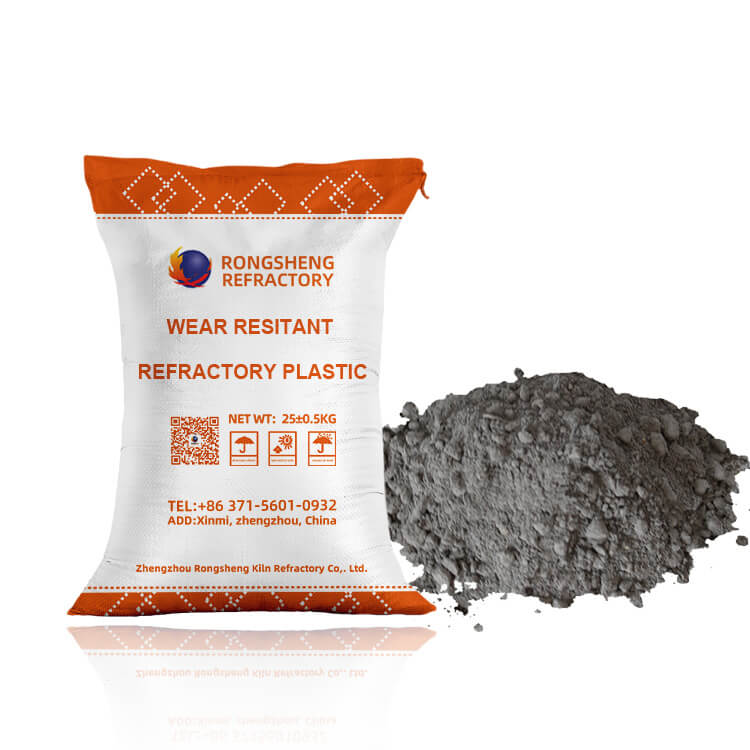
Application of Refractory Plastics in Soaking Furnaces
In the early stage of the application of refractory plastics in soaking furnaces, the furnace lining is damaged due to the breakage of the anchor bricks, and the service life is generally 12 to 15 months. Later, the shape and arrangement spacing of the anchor bricks were changed, which greatly improved the service life of the refractory plastic furnace lining. Generally, it is three times or more than the service life of the refractory brick lining. That is about five years.
China has repeatedly tried refractory plastic on the furnace walls and lids of large soaking furnaces, and its service life is basically the same as that of refractory brick furnace linings. On the walls of soaking furnaces in special steel plants, refractory plastic ramming furnace linings are often used. The service life is generally 4 years, and some are still in use.
The performance of refractory plastics used in soaking furnaces. These materials are also used on the furnace ends and tops of heating furnaces with good results. It should be pointed out that in Japan, it is common to use refractory plastics to build furnaces in soaking furnaces. In the early 1960s, Japan introduced this technology from the United States and developed rapidly from trial to trial production of new products. By the late 1960s, more than 95% of soaking furnace covers were lined with refractory plastic, and their service life was generally 2.0 to 2.5 years. Refractory plastics are also commonly used on furnace walls, with a service life of 3 to 1 year. After several minor repairs, its lifespan can reach more than 5 years. In the 1970s, the application of refractory plastics in soaking furnaces reached a finalized design and was directly supplied by manufacturers according to brand requirements.
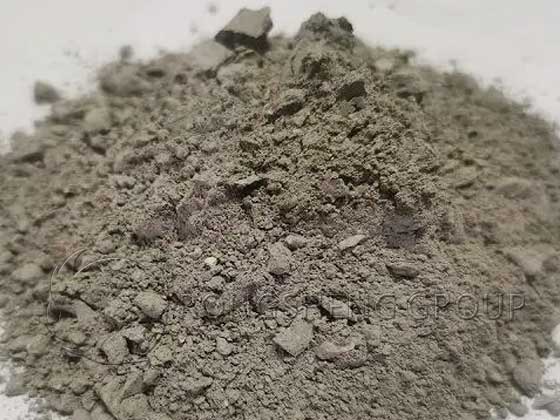
The Service Life of the Refractory Plastic Lining of the Soaking Furnace
The service life of the refractory plastic lining of the soaking furnace is closely related to the structure type of the furnace body. That is, the quality of the anchoring and hanging system directly affects the use effect of the furnace lining.
Anchor bricks and hanging bricks are movablely connected to the furnace shell or steel structure, and their main bodies are embedded in the refractory and plastic furnace lining, forming a unified whole. It can resist the inclination of the furnace wall, structural peeling, and abrasion damage caused by temperature and mechanical collision, thereby extending the service life of the furnace lining.
Anchor bricks and hanging bricks are generally made of high-aluminum materials with an Al2O3 content equal to or greater than 60%. The volume density is about 2.34 g/cm3, the compressive strength is greater than 400 kg/cm3, and the linear expansion after reheating at 1500°C is about 0.05%. Its cross-sectional size is 100×120 (or 180) mm. The length should be greater than the thickness of the furnace lining and the metal parts should be kept away from high-temperature areas or exposed to the air as much as possible to increase the life of the bricks and facilitate disassembly and repair.
The spacing of furnace wall anchor bricks is generally 400×400 mm or 500×500 mm. If the furnace wall is high, supports can be installed appropriately to enhance stability. Supports are divided into two types: metal and non-metal. When installed, it must be fixed and kept away from the working layer of the furnace wall. The anchor bricks for the furnace wall around the burner are best arranged in a plum blossom shape, and metal anchors can be added if necessary.
The spacing of furnace roof hanging bricks is generally equivalent to the thickness of the furnace roof lining, and the common size is 300×300 mm. The hanging bricks are hung on metal tie beams using metal parts and are firmly fixed with wooden deeds during construction. A gap of 5 mm should be left between the bottom of the hanging bricks and the formwork so that the hanging bricks can be stressed evenly after the formwork is removed and to prevent damage to the furnace lining.
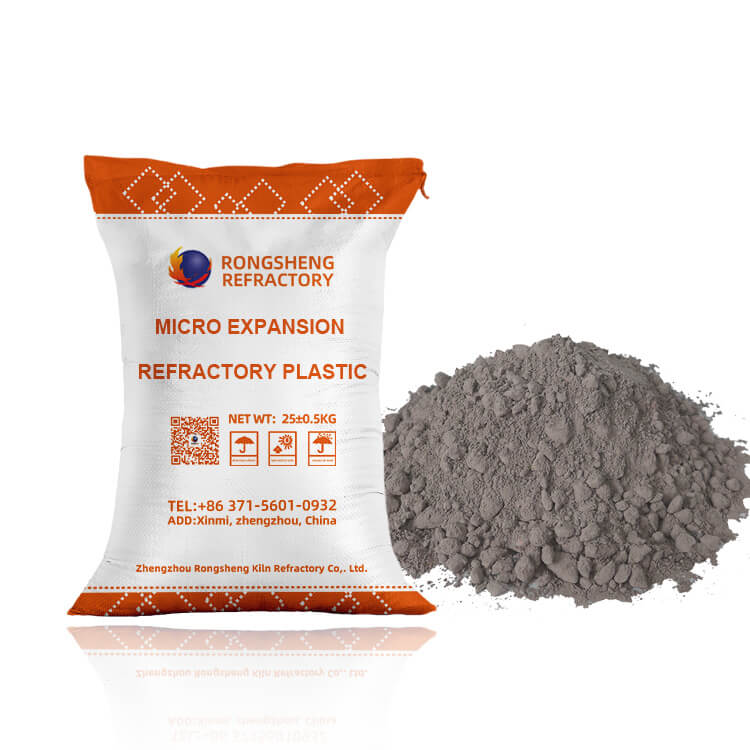
Configuration of Refractory Plastic Lining of Soaking Furnace
The spacing of hanging bricks on the flat roof of the furnace cover is 300×300 mm, and the spacing on the sloped roof part is smaller. It is made of refractory plastic with an Al2O3 content of 45% and a thickness of 230 mm. A 50 mm thick lightweight refractory castable is poured on the upper surface as a heat insulation layer. The furnace mouth is built with high-aluminum bricks with an Al2O3 content of 60%, or it can be made of refractory plastic of the same material. The spacing of the furnace wall anchor bricks is 400×450 mm, the total thickness of the side walls is 645 mm, of which the insulation board is 65 mm, and the partition wall thickness is 456 mm. The bottom of the furnace wall is made of refractory plastic with an Al2O3 content of 80% to resist erosion by slag. The remaining parts are made of clay refractory plastic with an Al2O3 content of 45%. The working layer of the furnace bottom is made of clay bricks, and the insulation layer is made of lightweight clay bricks, diatomaceous earth bricks, and asbestos boards, with a total thickness of 380 mm.
Construction Quality of Refractory Plastics
The construction quality of refractory plastics has a direct impact on the service life of the furnace lining, and it must be operated in strict accordance with technical regulations. Before construction, various refractory materials, machinery, and tools should be prepared to ensure normal construction. The pounding of refractory plastics should be carried out continuously. If there is a temporary interruption, cover it tightly with plastic sheeting to prevent moisture from evaporating. The ramming direction should be parallel to the hot surface of the furnace lining construction body, that is, the furnace wall should be rammed vertically and the furnace top should be rammed horizontally. The walking speed of the hammer head should ensure that the ramming surfaces can overlap each other by about 1/2, and the hammering should be repeated 3 to 5 times. The refractory plastic construction layers must be fully integrated and uniform in texture, with no gaps or leaks allowed.
The refractory plastic can be rammed into a place where the anchor bricks will be placed. First, use a wooden or metal mold similar in shape to the anchor bricks to drive it into the plastic lining, then take out the mold and insert the anchor bricks. Then continue to pound the refractory plastic to tightly bond it with the anchor bricks. Otherwise, the anchor bricks will not be able to perform the anchoring function and may cause smoke and fire easily.
A non-penetrating expansion joint should be left at the corner of the furnace wall with a width of 10 to 20 mm. Use wooden boards or plastic corrugated boards as caulking materials to burn them in the oven.
After the entire furnace lining is pounded, it needs to be naturally cured for 24 hours before the formwork is removed and the working surface is renovated. Ventilation holes are drilled with a diameter of 6 to 8 mm, a spacing of 100 to 200 mm, and a depth of 2/3 of the thickness of the construction body. Briefly avoid the anchors and use a cutter to cut expansion joints. The width of the joint is 5 mm and the depth is 40 to 60 mm. The distance depends on the performance of the furnace material, generally 2 to 4 meters. It should be pointed out that it is also feasible to directly use plywood or plastic corrugated boards as expansion joints during construction.
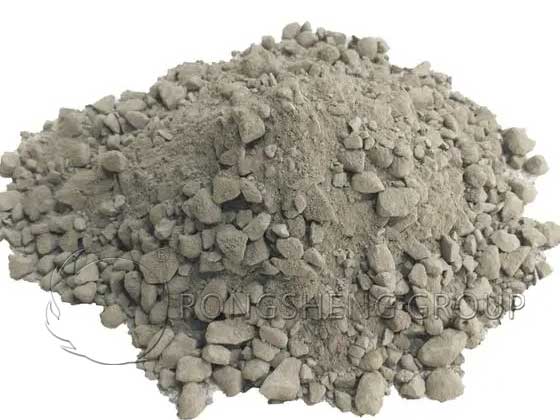
After the construction is completed, the site is cleaned and the oven is carried out within a week. The figure below shows the oven curve of the soaking furnace (220 hours in total). Before 700℃, insert a temporary gas pipe through the slag hole at the bottom of the furnace for baking. There should be a gap in the furnace cover and the flue gate should be closed. After reaching 700°C, close the furnace cover, slightly open the flue gate, ignite the working burner and continue drying until the operating temperature is reached before installing steel for production.
Large-scale refractory plastic prefabricated blocks are generally hoisted mechanically, while small ones are assembled manually. The spacing between anchor bricks is basically the same as mentioned above. When the first layer of anchor bricks is laid, all or at least less than the anchor bricks should be refractory and plastic pounded on site to make the furnace wall form a whole. After the construction of this layer is completed and leveled, hoisting of prefabricated blocks will continue.
RS Refractory Plastic Factory
Using refractory plastic prefabricated blocks to make the furnace wall of the soaking furnace have a service life basically the same as that of the plastic furnace wall that is pounded on site. The speed of furnace construction is increased and the unit price of the project is reduced. Rongsheng refractory material manufacturer can provide high-quality refractory plastics for high-temperature industrial furnaces such as soaking furnaces. Equipped with PA80 glue. RS manufacturer’s refractory plastics can be customized according to the working conditions of high-temperature industrial furnaces. For example, wear-resistant refractory plastics, high-aluminum and high-strength corundum refractory plastics, micro-expansion refractory plastics, and silicon carbide refractory plastics.
More Details