Product Characteristics:
1. Silicon carbide foam ceramic filter using German imported polyurethane foam sponge as a carrier, silicon carbide mainly squeezed into the foam sponge, and then squeeze out the slurry,
the slurry around the foam fiber, after drying, baking at high temperature, polyurethane thermal
decomposition, leaving foam ceramic products, namely silicon carbide foam ceramic filter.
The silicon carbide foam ceramic filter, with the three- dimensional mesh interconnection structure of foam sponge, can make metal liquid reflect rectification, mechanical screening, filtration cake, adsorption and other filtration mechanisms to effectively improve the purity of metal liquid, reduce waste rate, reduce mechanical processing loss, thus improve production efficiency and reduce production cost.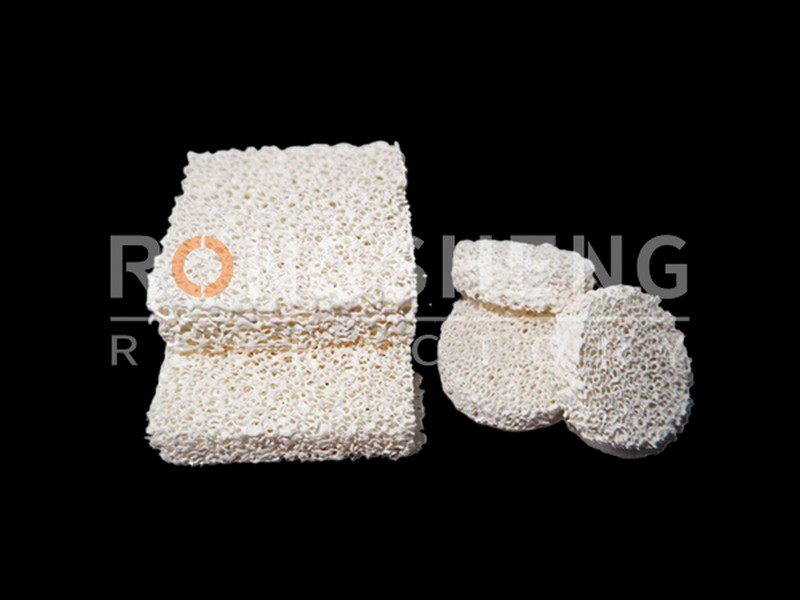
Composition of product |
Silicon Carbide,AL2O3,SiO ect |
Color |
Grey,Dark Grey |
Using Temperature |
≤1550℃ |
Number of hole density PP(holes per square inch) |
10,15,20,30 |
Porosity |
85%-90% |
CMOR Mpa |
≥1.5Mpa(Industry Standard 1.0Mpa) |
Bulk Density |
0.4g/cm3~0.5g/cm3 |
Square specification(mm) |
Max filtering capacity(kg) |
Normal metal fluid flow velocity(kg/s) |
Round Specification(mm) |
Max filtering capacity(kg) |
Normal metal fluid flow velocity(kg/s) |
Ductile cast iron |
Ash cast iron/copper-aluminum castings |
Ductile cast iron |
Ash cast iron/copper-aluminum castings |
Ductile cast iron |
Ash cast iron/copper-aluminum castings |
Ductile cast iron |
Ash cast iron/copper-aluminum castings |
40*40*22 |
32 |
64 |
3 |
4 |
Φ40*22 |
25 |
50 |
2 |
3.5 |
50*50*22 |
50 |
100 |
4 |
6 |
Φ50*22 |
35 |
70 |
3 |
4.5 |
60*60*22 |
72 |
144 |
5 |
8 |
Φ60*22 |
50 |
100 |
4.2 |
6.5 |
75*50*22 |
75 |
150 |
6 |
9 |
Φ70*22 |
75 |
150 |
5.5 |
8.8 |
100*50*22 |
100 |
200 |
8 |
12 |
Φ80*22 |
100 |
200 |
7.2 |
11 |
75*75*22 |
110 |
220 |
9 |
14 |
Φ90*22 |
120 |
240 |
9 |
14 |
80*80*22 |
150 |
300 |
12 |
18 |
Φ100*22 |
140 |
280 |
11 |
17 |
100*100*22 |
200 |
400 |
16 |
24 |
Φ110*22 |
190 |
380 |
13 |
20 |
150*100*22 |
300 |
600 |
24 |
36 |
Φ120*22 |
230 |
460 |
16 |
25 |
150*150*22 |
450 |
900 |
36 |
54 |
Φ150*22 |
350 |
700 |
25 |
30 |
2.Alumina Foam Ceramic Filter
Alumina ceramic foam filter is a new type of low density, high porosity and with three dimensional network skeleton structure of the filter. And widely used in aluminum process industry for molten aluminum filtering, so as to improve aluminum quality.
Alumina ceramic foam filter can effectively removes non-metal solid mixture from aluminium and aluminium alloy fusant, reduce trapped gas and provide laminar flow and then the filtered metal is significantly cleaner. Cleaner metal results in higher-quality castings, less scrap, and fewer inclusion defects, to improve the quality of aluminum alloy and other non-ferrous alloy casting, all of which contribute to reduce casting cost, its maximum service temperature 1200° C.
Alumina ceramic foam filter has the advantages of high porosity, high mechanical strength, stable chemical property, strong corrosion-resistant, high adsorption rate, excellent filtering functions and thermal shock resistance. It is mainly used for purification process of aluminum, aluminum alloy, and other nonferrous alloy production, can also be used as gas-solid, liquid-solid separation medium, catalyst carrier, burner and sound-absorbing and environmental protection fields.
Alumina ceramic foam filter is equipped with a gasket on the edges; the gasket assures the proper and tight position of the filter within the filter box. There are different types of gasket available, e.g. ceramic fiber gasket etc., also can provide alumina ceramic foam filter without gasket. These types of filters have been favored by customers from Europe and the United States for years.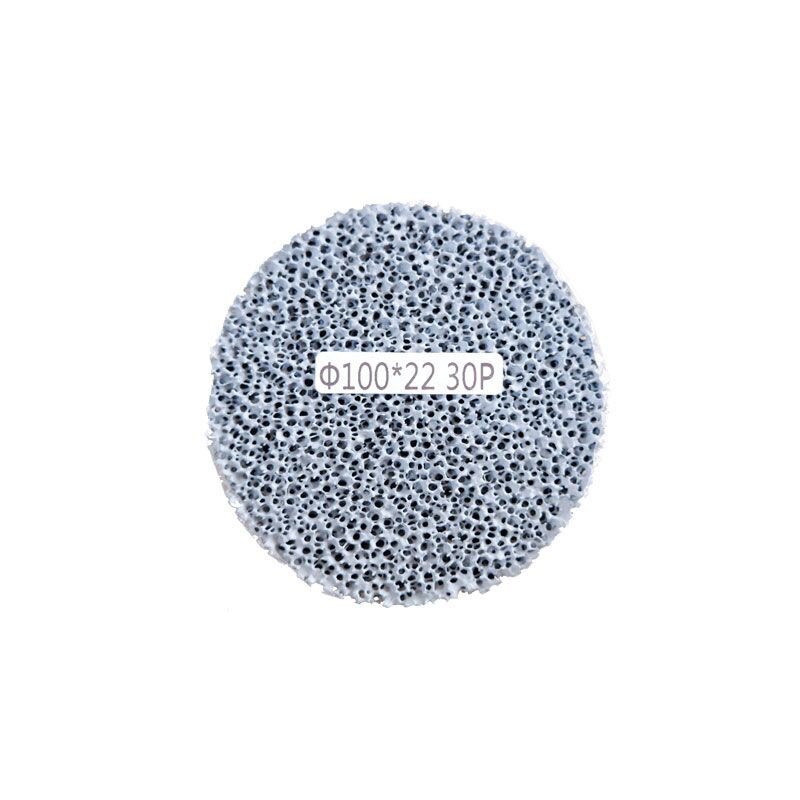
Application of Alumina ceramic foam filter:
Alumina ceramic foam filter is mainly applied to the aluminum and aluminum alloys fusant filter equipment of continuous casting, half-continuous casting, gravity casting, and low pressure casting, also applied to other non-ferrous metal precision casting, gas-solid and liquid-solid separation medium, high temperature gas filter, chemical filling, sound absorbing material and catalysis carrier etc.
Porosity(%) |
80-90% |
Working Temperature |
≤1100℃ |
Bending Strength (Mpa) |
0.6 |
Compression Strength (Mpa) |
0.8 |
Thermal Shock Resistance |
1100℃—room temperature 6 times |
Bulk Density |
0.35-0.45 g/cm3 |
3.Zirconia Foam Ceramic Filter:
Product Performance:
1.Adjust the metal flow rate through rectification to reduce secondary inclusion and pores.
2.Reduce casting inclusion and reduce casting waste and welding repair rate.
3.Improve the surface quality and mechanical properties of the castings.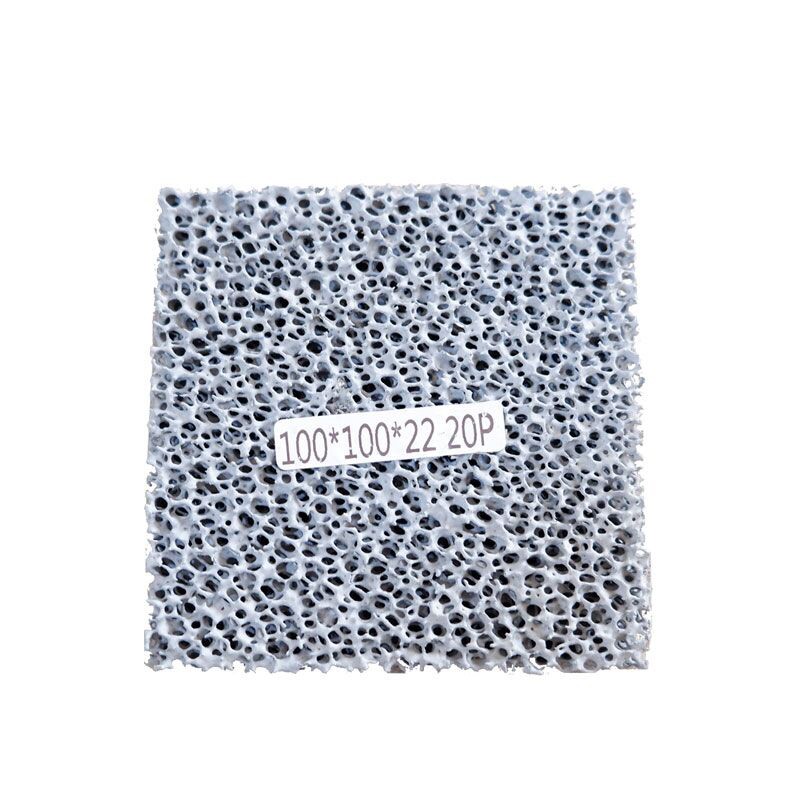
Application of Zirconia Foam Ceramic Filter:
Filtration of stainless steel, carbon steel and large castings.
L * W * T / Diameter *thick (mm) |
Filter capacity (kg) |
The pouring flow (kg/s) direct channel is 300mm high |
High degree of deoxygenation |
Low degree of deoxygenation |
Carbon-based steel castings |
Stainless steel casting pieces |
50Dx20 |
30 |
90 |
2.0 |
3.0 |
70Dx25 |
60 |
175 |
3.8 |
5.7 |
90Dx25 |
95 |
285 |
6.4 |
9.5 |
125Dx30 |
185 |
550 |
12.2 |
18.4 |
150Dx30 |
265 |
795 |
17.7 |
26.5 |
50x50x20 |
35 |
110 |
2.5 |
3.7 |
50x75x25 |
55 |
170 |
3.7 |
5.6 |
75x75x25 |
85 |
255 |
5.6 |
8.4 |
100x100x25 |
150 |
450 |
10.0 |
15.0 |
125x125x30 |
235 |
700 |
15.6 |
23.4 |
150x150x30 |
340 |
1010 |
22.5 |
33.7 |
More Details